5 Whys
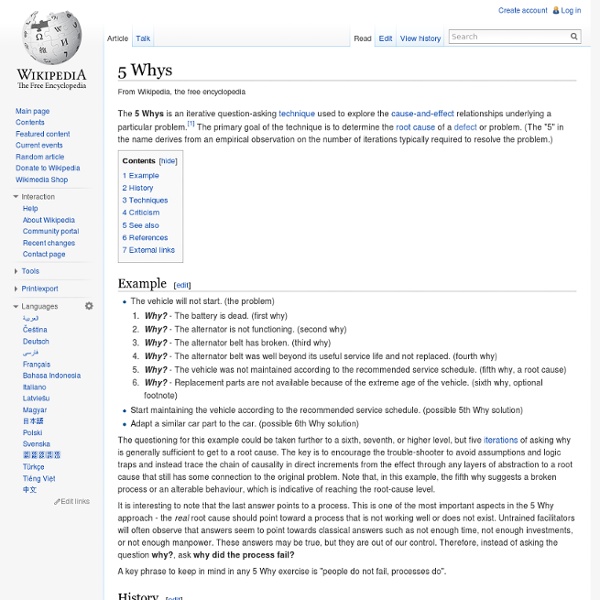
The 5 Whys is an iterative question-asking technique used to explore the cause-and-effect relationships underlying a particular problem.[1] The primary goal of the technique is to determine the root cause of a defect or problem. (The "5" in the name derives from an empirical observation on the number of iterations typically required to resolve the problem.) Example[edit] The vehicle will not start. (the problem)Why? - The battery is dead. The questioning for this example could be taken further to a sixth, seventh, or higher level, but five iterations of asking why is generally sufficient to get to a root cause. It is interesting to note that the last answer points to a process. A key phrase to keep in mind in any 5 Why exercise is "people do not fail, processes do". History[edit] The technique was originally developed by Sakichi Toyoda and was used within the Toyota Motor Corporation during the evolution of its manufacturing methodologies. Techniques[edit] Criticism[edit] See also[edit]
Eight Disciplines Problem Solving
Eight Disciplines Problem Solving (8D) is a method used to approach and to resolve problems, typically employed by quality engineers or other professionals. Its purpose is to identify, correct and eliminate recurring problems, and it is useful in product and process improvement. It establishes a permanent corrective action based on statistical analysis of the problem (when appropriate) and focuses on the origin of the problem by determining its root causes. Although it originally comprised eight stages, or 'disciplines', it was later augmented by an initial planning stage. The 8D follows the logic of the PDCA cycle. The disciplines are: D0: Plan: Plan for solving the problem and determine the prerequisites. D1: Use a Team: Establish a team of people with product/process knowledge. D2: Define and describe the Problem: Specify the problem by identifying in quantifiable terms the who, what, where, when, why, how, and how many (5W2H) for the problem. History[edit] Ford's perspective[edit]
Fix it twice
Avram Joel Spolsky (born 1965) is a software engineer and writer. He is the author of Joel on Software, a blog on software development. He was a Program Manager on the Microsoft Excel team between 1991 and 1994. He later founded Fog Creek Software in 2000 and launched the Joel on Software blog. In 2008, he launched the now-successful Stack Overflow programmer Q&A site in collaboration with Jeff Atwood. Using the Stack Exchange software product which powers Stack Overflow, The Stack Exchange Network now hosts over 100 Q&A sites. Biography[edit] Spolsky grew up in Albuquerque, New Mexico and lived there until he was 15.[2] He then moved with his family to Jerusalem, Israel, where he attended high school and did his military service as a paratrooper.[2] He was one of the founders of Kibbutz Hanaton in Upper Galilee.[3] In 1987, he returned to the United States to attend college. In 2011, Spolsky launched Trello, an online project management tool inspired by Kanban methodology.[10]
Root Cause Analyse – vermeiden Sie das wiederholte Auftreten gleicher Fehler! | Qualitätsmanagement
Und täglich grüßt das Murmeltier! Dieser Vergleich pointiert die Situation in vielen Organisationen. Jeden Tag erleben die Mitarbeiter die selben oder ähnliche Fehler aufs Neue. Fehler übergeordneter Funktions-Ebenen einer Organisation (= Entscheidungsträger) lösen über „kurz oder lang” Störungen auf der Ausführungsebene aus, denn - die Entscheidungen und Maßnahmen des Top Management definieren den gestalterischen Rahmen. - das operative Management gestaltet danach die Arbeitsbedingungen, plant, steuert und kontrolliert. - die Menschen und Systeme funktionieren unter diesen Arbeitsbedingungen. Aufbauend auf dieser Erkenntnis, sollten Sie bei Ihrer Reaktion auf unerwünschte Ereignisse (Unfälle, fehlerhafte Leistungen, …) die folgenden drei Ebenen der Ursachenanalyse unterscheiden: 1. Ermittlung des Hergangs durch Darstellung der Ereignisketten, mit dem Ziel der Abstellung der direkten Ursache. 2. Welche Abweichung von der Normalität war ursächlich für den/die Fehler: - Unwissenheit der Akteure.
Related:
Related: