Six Sigma - What is Six Sigma?
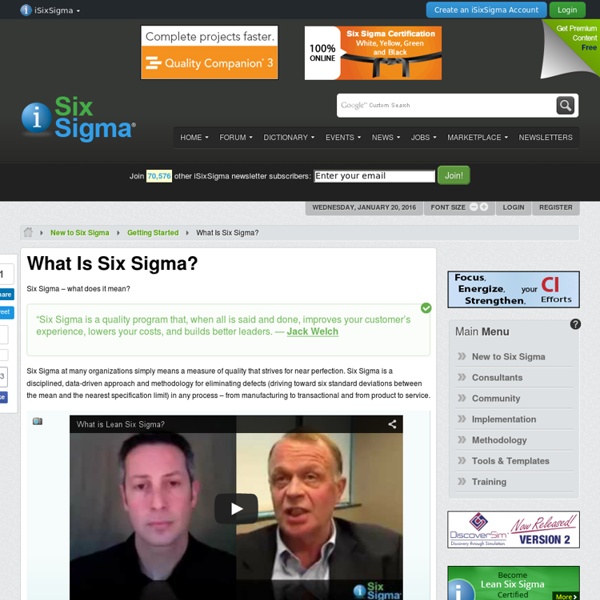
Six Sigma – what does it mean? “Six Sigma is a quality program that, when all is said and done, improves your customer’s experience, lowers your costs, and builds better leaders. — Jack Welch Six Sigma at many organizations simply means a measure of quality that strives for near perfection. Six Sigma is a disciplined, data-driven approach and methodology for eliminating defects (driving toward six standard deviations between the mean and the nearest specification limit) in any process – from manufacturing to transactional and from product to service. The statistical representation of Six Sigma describes quantitatively how a process is performing. To achieve Six Sigma, a process must not produce more than 3.4 defects per million opportunities. The fundamental objective of the Six Sigma methodology is the implementation of a measurement-based strategy that focuses on process improvement and variation reduction through the application of Six Sigma improvement projects.
Introduction to Problem Solving
.:VirtualSalt Robert Harris Version Date: July 2, 1998 Regardless of what they do for a living or where they live, most people spend most of their waking hours, at work or at home, solving problems. Most problems we face are small, some are large and complex, but they all need to be solved in a satisfactory way. Before we look at the area of problem analysis and solution, though, let's take a few moments to think about just what we mean by a problem. What is a Problem? One of the creative thinker's fundamental insights is that most questions have more than one right answer and most problems have more than one solution. 1. Developing a positive attitude toward problems can transform you into a happier, saner, more confident person who feels (and is) much more in control of life. 2. 3. The Importance of Goals in Problem Solving As you read these definitions, I hope you noticed that they all include the ideas of goals and ideal states. What is a Solution? Stop It Prevent It. Eliminate It. I.
Six Sigma
The common Six Sigma symbol Six Sigma is a set of techniques and tools for process improvement. It was developed by Motorola in 1986.[1][2] Jack Welch made it central to his business strategy at General Electric in 1995.[3] Today, it is used in many industrial sectors.[4] Six Sigma seeks to improve the quality of process outputs by identifying and removing the causes of defects (errors) and minimizing variability in manufacturing and business processes. The term Six Sigma originated from terminology associated with manufacturing, specifically terms associated with statistical modeling of manufacturing processes. Doctrine[edit] Six Sigma doctrine asserts that: Features that set Six Sigma apart from previous quality improvement initiatives include: The term "six sigma" comes from statistics and is used in statistical quality control, which evaluates process capability. "Six Sigma" was registered June 11, 1991 as U.S. Methodologies[edit] DMAIC[edit] The DMAIC project methodology has five phases:
Related:
Related: